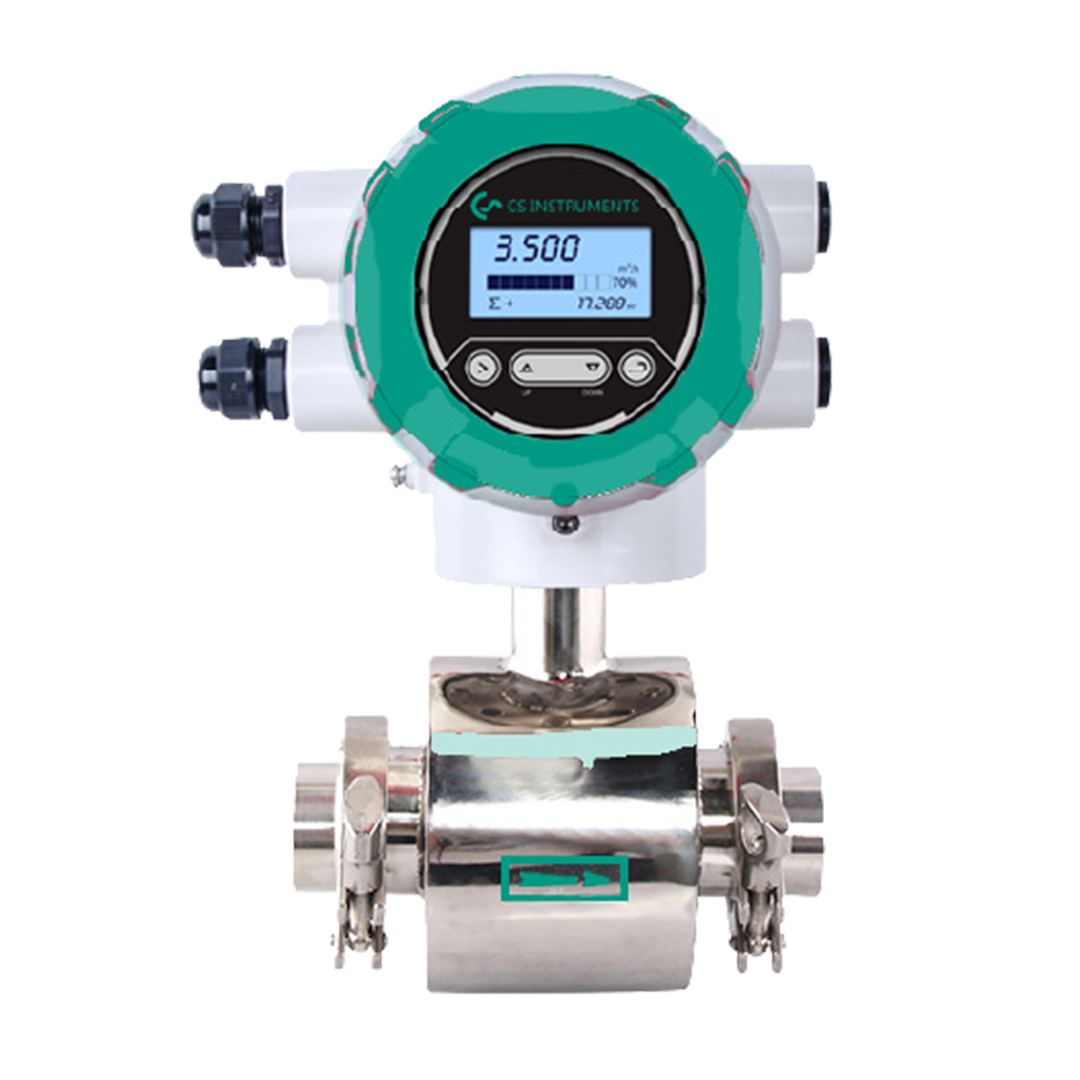
WA 500 Caudalímetro electromagnético
Puede medir el flujo de fluido en direcciones hacia adelante y hacia atrás.
1. Introducción
En el contexto industrial actual, la medición precisa y la eficiencia energética son fundamentales para optimizar costos y garantizar la calidad del producto. En una fábrica de refrescos, la gestión eficiente de la energía y la calidad del aire comprimido no solo contribuye a la reducción de costos operativos, sino que también asegura la integridad del producto final. Este caso práctico aborda las necesidades de una fábrica de refrescos en términos de eficiencia energética, reparto de costos de gases y calidad del aire.
2. Descripción del caso y problemas principales
El cliente utiliza una sala de compresores equipada con cuatro compresores de diferentes capacidades y características: tres de 55 kW y uno sin aceite de 22 kW. En la sala de compresores no se realiza monitoreo de las variables críticas, lo que lleva a una falta de datos sobre el rendimiento y la eficiencia energética de los compresores. La tasa de fugas en el sistema de aire comprimido es del 25%, lo que genera un potencial de desperdicio energético y un costo adicional de aproximadamente 35,000€ anuales.
En las enfriadoras utilizan agua para sus procesos de producción, pero no dispone de datos sobre la eficiencia de cada una. Lo que supone un desconocimiento del gasto individual de cada una e ineficiencia.
En los conductos de aire comprimido a pesar de los filtros, aún continúan habiendo partículas indeseadas que contaminan las líneas de producción.
La mala gestión del reparto de costes en CO2 en los sistemas producían mermas y por tanto pérdidas económicas.
3. Solución para el Caso Práctico
Se propone la implementación de un sistema integral de monitoreo y registro para controlar todos los parámetros en relación con los problemas mencionados. Este sistema permitirá:
1. Monitorear en tiempo real la eficiencia energética de los compresores y enfriadoras.
2. Medir y controlar el flujo de aire comprimido y CO2.
3. Asegurar la calidad del aire comprimido en contacto con el producto mediante sensores de partículas y vapor de aceite.
4. Generar informes automáticos y alarmas por desviaciones, facilitando la toma de decisiones y el mantenimiento preventivo.
4. Equipos utilizados
Para abordar los desafíos mencionados, se utilizan diversos equipos de medición:
- Videoregistrador DS 500: Para la supervisión y registro de datos de eficiencia energética y calidad del aire.
- Caudalímetro de inserción VA 500: Para medir el flujo de aire comprimido.
- Sensor de punto de rocío: Esencial para secadores de refrigeración.
- Sensores de presión: Para medir hasta 16 bar.
- Medidores de energía eléctrica: Para cada compresor.
- Sensores de partículas y vapor de aceite residual: Para asegurar la calidad del aire comprimido.
- Caudalímetro electromagnético modelo WA 500: Para la monitorización del agua en enfriadoras.
- Sondas de temperatura de inmersión: Para tuberías de impulsión y retorno.
- Medidores de energía eléctrica y centralita DS 400: Para registrar el COP de las enfriadoras.
- Caudalímetro modelo VA 520: Para medir el flujo de CO2 en líneas de producción.
5. Beneficios
La implementación de esta solución proporciona múltiples beneficios:
- Reducción de costos: Potencial ahorro de 35,000€ anuales por la reducción de fugas en el sistema de aire comprimido.
- Mejora de la eficiencia: Optimización del rendimiento de compresores y enfriadoras.
- Calidad del producto: Aseguramiento de la calidad del aire comprimido, minimizando el riesgo de contaminación.
- Control y análisis: Acceso continuo a datos, informes automáticos y alarmas, permitiendo una gestión proactiva de los recursos energéticos y del aire comprimido.
Este caso práctico destaca la importancia de un monitoreo preciso y eficiente de los recursos energéticos y la calidad del aire en una fábrica de refrescos, demostrando cómo una solución integral puede generar significativos beneficios económicos y de calidad.