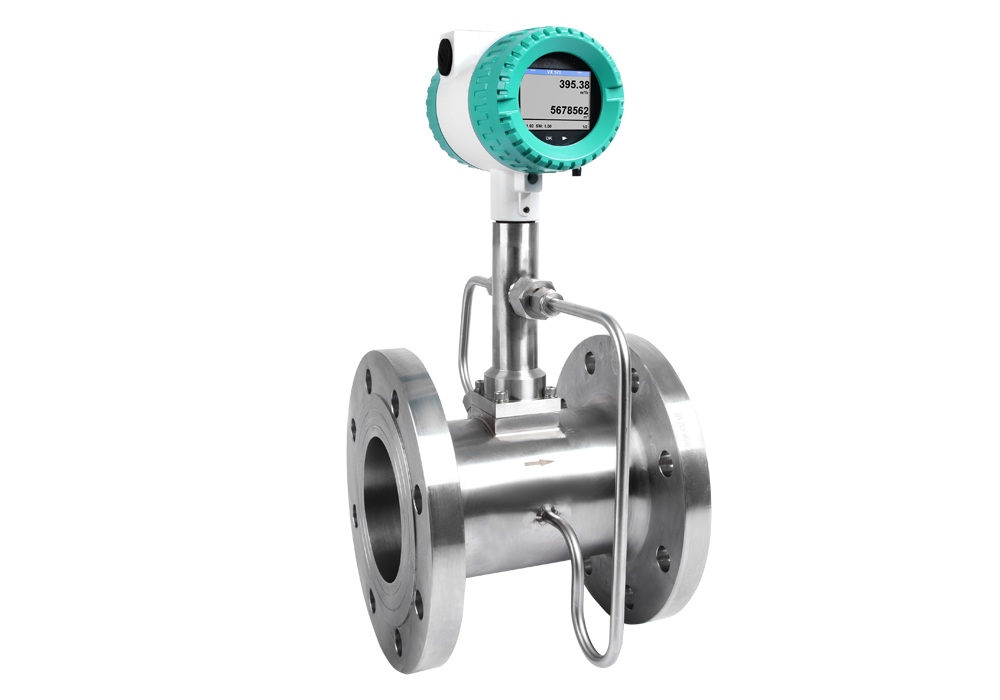
VX 570 - Vortex Flow sensor for steam, gases and liquids
The high-precision all-rounder with integrated pressure and temperature compensation
Industrial turbo compressors are Compressed air generators that are often used in industries such as the automotive industry, the iron and steel industry, glass production and the textile industry. Due to the high Energy consumption of turbo compressors, the operating costs are very high. This results in the need to continuously measure the flow of Compressed air produced and monitor the Efficiency of the Compressors.
Thanks to Vortex flow meters, continuous monitoring of the compressed air flow of turbo compressors is very easy. Measuring, recording and visualizing the data is handled by CS INSTRUMENTS systems.
The high-precision VX 570 Vortex flow meter from CS INSTRUMENTS provides you with the data you need to optimize your consumption and improve the system's sustainability indicators. You can easily monitor the consumption of different fluids with just one VX 570 flow meter, and you can monitor this data in a computer environment thanks to the DS500 Chart recorder and CS INSTRUMENTS Basic Software, also offered by CS INSTRUMENTS.
To optimize the energy costs of the system, the turbocompressor must be operated with the highest possible Efficiency. To achieve this efficiency, it is necessary to monitor and report the flow rate of the Compressor. If a technical problem occurs with the flow rate, it should be quickly identified and rectified. This process can be easily tracked with the CS INSTRUMENTS VX 570 Flow sensor. For a very small investment, you can save thousands of euros in energy costs incurred each year due to Losses in the Efficiency of your Compressor.
The VX 570 flow sensor is a precision measuring device with a very large Measuring range between 2 - 70 m/s. Furthermore, it is not only suitable for air flows, but also for gas compositions and Mixed gases, unclear or variable compounds. Thanks to Vortex technology, it can also measure liquids and vapors. Instantaneous flow, metering values (consumption) as well as flow velocity, temperature and line pressure values are also measured and monitored.
The display housing of the Flow meter is made of an aluminum alloy to withstand the harshest conditions. The inner material of the liquid contact is made of high quality stainless steel to withstand aggressive environments. Durability is the top priority of the VX570, so it contains no moving parts. Thanks to this robust construction, it is maintenance-free.
The VX 570 flow meter measures the actual volume flow and mass flow. Thanks to integrated pressure and temperature compensation, it also calculates the normal/standard volume flow. External Temperature and Pressure sensors or an additional corrector are not required. This minimizes the measurement error and eliminates additional investment costs.
VX 570, uses the most innovative measuring principles thanks to CS INSTRUMENTS' many years of experience and technical knowledge in Compressed air and Gas measurement. It is designed to provide reliable measurement results even under rapidly changing Temperature, Pressure and Flow conditions.
Another decisive advantage of the VX570 is its vibration independence thanks to the advanced integrated vibration measurement and filtering.
For the Efficiency measurement of turbo compressors, the data measured by Flow meters such as Flow, Consumption, Pressure, Velocities and Temperature should be recorded and visualized in the form of graphs and tables.
All sensors, including Flow meters and Ambient conditions sensors, used in the compressor room are connected to the DS 500 Chart recorder. In this way, the entire system is recorded at a single point and the Measured values are recorded. On the 7-inch color touch screen, the user can see values such as Compressor Flow rates, Pressure and m3 air volume produced at a glance.
The data recorded in the DS 500 Chart recorder can be easily exported. Or monitored in real time via the DS 500's USB and Ethernet connection. Creating weekly, monthly and annual consumption reports is particularly easy with the help of the CS Basic PC software. All diagrams can also be evaluated thanks to CS Basic.
Industrial turbo compressors are used to cover the enormous air consumption of large industrial plants. While the most commonly used screw compressor has a maximum motor output of 315 kW, 2000 kW motors are not uncommon in the world of turbocompressors.
The energy consumed by such a turbocompressor per year is around 16 million kWh. It is easy to calculate that the annual energy consumption costs amount to over 3 million euros.
It is crucial to measure the compressed air throughput that is achieved in return for such enormous energy costs.